Build Priority Chaos: How to End the Daily Confusion in Hardware Manufacturing
"What should we build today?"
Five little words that kick off a world of trouble in hardware companies everywhere.
Walk into any manufacturing morning meeting and you'll see the drama unfold. The sales team points to promised delivery dates and customer relationships. Engineers remind everyone about technical requirements and quality standards. Meanwhile, the manufacturing team gestures at what's actually sitting in inventory, wondering how they're supposed to build products with parts that haven't arrived yet.
Each team has a perfectly good point. Put them all together though, and you've got what we call "Build Priority Chaos" — when everyone has a different idea of what matters most.
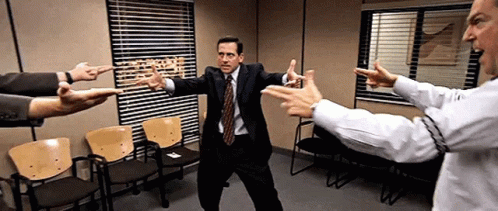
We've been chatting with hardware teams about this problem, and it turns out almost everyone struggles with it. One team told us they spend nearly an hour each day just figuring out what to build — only to change their minds completely when an unexpected shipment arrives after lunch. Another mentioned they've given up on their official priority list entirely and just keep their own secret versions.
If you're nodding along right now, know you're not alone. The good news? Some teams have figured out how to tame this chaos, and they're sharing their secrets.
The Daily Struggle of Shifting Priorities
So what makes this whole "what to build" question so hard to answer? From our chats with hardware teams, three culprits keep showing up:
First, parts show up whenever they feel like it. The critical component you've been waiting six weeks for? Still "in transit." Those specialty screws nobody urgently needs? They just arrived in triple quantity. Suddenly your planned schedule looks about as relevant as last year's calendar.
As one engineer put it to us: "Our production schedule has the life expectancy of a mayfly. Four hours tops before something blows it up."
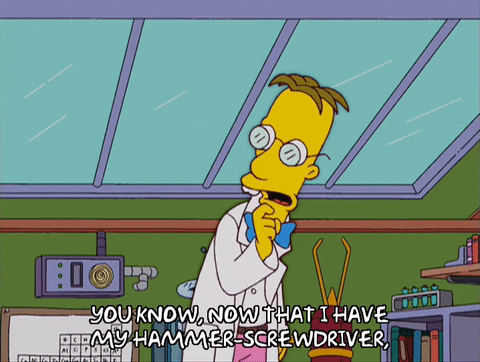
Second, engineering changes pop up like dandelions after rain. The "finished" design suddenly needs one more tweak. That "minor update" requires completely new testing. The "final version" somehow reaches version 12.0 before anyone ships a thing.
Third, customer deadlines are apparently written in water, not stone. The "absolutely can't miss" date from last week? The customer just called and needs it sooner. Or later. Or differently. Meanwhile, the sales team has promised rush delivery to yet another "most important customer we have."
The cost of all this chaos isn't just wasted time — though hardware teams report spending countless hours in priority debates. It's also the constant whiplash of changing directions. As one operations manager shared: "My team's productivity takes a hit every time we switch priorities. And we switch priorities roughly... let me check my watch... every three hours."
Finding a Better Way: The Single Source of Truth
So how do successful hardware teams escape this chaos? Based on our conversations with manufacturing leaders who've solved this challenge, three key elements consistently emerge:
1. They use a clear recipe for priorities
Instead of arguing about what "feels" important, successful teams use a simple formula everyone agrees on. Their priority calculations typically mix together:
- How soon a customer needs their order
- How much money the order is worth
- How important the customer relationship is
- What specialized equipment or skills are needed
- How this build affects other products
The magic isn't in the exact recipe — it's that everyone agrees on it. When something changes, they don't restart the whole priority debate. They just run the new information through their formula.
2. Everyone sees the right information
The best systems don't overwhelm teams with every piece of data — they show each team exactly what they need to know:
- Manufacturing sees which builds have all required components available
- Engineering knows which designs need urgent attention
- Supply chain focuses on critical parts that could delay priority orders
This targeted visibility eliminates confusion and debate. When everyone sees the information that matters for their role, the team naturally aligns around what's truly important today.
3. They make priorities visually obvious
Instead of complex spreadsheets and databases, successful teams use simple visual signals that anyone can understand at a glance.
One team we talked to uses a straightforward color system: green builds have all parts available, yellow builds are coming soon but missing components, red builds have urgent deadlines but critical blockers.
When priorities are this obvious, teams spend their time building products instead of debating what to build.
The Transformation of Priority Management
What happens when teams get this right? Based on what we've heard from manufacturing teams, the changes are pretty dramatic:
Morning meetings transform from painful priority debates into quick check-ins. Instead of arguing about what to build, teams focus on helping each other overcome specific challenges. One operations manager told us their daily meeting went from 45 minutes of circular debate to a focused 10-minute huddle.
The finger-pointing stops too. When a critical part is delayed, the system automatically adjusts priorities and notifies everyone. No more blame games about who didn't communicate what to whom.
But the biggest change? Orders actually ship when promised. Multiple teams reported massive improvements in on-time delivery after implementing clear priority systems – jumping from barely 60% to over 90% on-time delivery within months.
The psychological benefits are just as important. When people know exactly what they should be working on, the constant second-guessing and stress disappears. As one production lead put it: "The constant priority debates were exhausting everyone. Now we only argue about the important stuff — like who ate the last pizza in the break room."
A New Reality: From Chaos to Clarity
When priority chaos disappears, the benefits spread throughout the company:
The finance team suddenly finds they can predict cash flow more accurately since products actually ship when expected.
Sales reps can have honest conversations with customers about realistic timelines instead of making promises they know will probably be broken.
The quality team can focus on genuine process improvements instead of rushing around putting out priority fires.
And operations can actually scale as you grow, because you're not constantly reinventing your priority system with each new order.
The cultural transformation is equally powerful. When priorities are clear, the entire workplace dynamic shifts. Cross-functional interactions stop feeling like territorial negotiations and start resembling actual teamwork. You hear less "That's not our department's problem" and more "Let's figure this out together." Teams invest their energy in solving technical challenges rather than debating whose deadline matters most.
Taking the First Step Toward Priority Clarity
Want to know if your team has a priority problem? Ask yourself:
- How much time do you spend each day figuring out what to build?
- How often do your priorities completely change between morning and afternoon?
- What percentage of orders actually ship when originally promised?
- Could someone from sales, engineering, and manufacturing independently make the same list of today's top three priorities?
If your answers reveal chaos (and they probably do), take heart. Most hardware teams struggle with this exact problem. The good news is that fixing it doesn't require a massive organizational overhaul or an expensive enterprise system. It starts with creating a simple, visible priority framework that everyone understands and trusts.
The most successful hardware companies know that solving priority chaos isn't just about efficiency – it transforms how teams work together, how customers see your company, and ultimately, how successfully you can grow your operations.
At Bread Board Foundry, we've built Pretzel specifically to solve build priority chaos for small hardware teams. Our system creates a single source of truth that automatically sorts priorities based on parts availability, engineering readiness, and customer deadlines – all without the complexity of enterprise systems.
Learn more at pretzel.today.
Member discussion